TOOL LIFE
Titanium Tool Life
When it comes to profitability in the machining of titanium components, tool life is one of the key factors. In order to remain profitable, manufacturers must select the appropriate equipment with an effective coolant system.
In a typical machining process, heat generated within the cutting zone is dispersed through the part, tool and surrounding environment; however, this is not the case for titanium. Due to the material’s low thermal conductivity, a higher level of heat is concentrated directly onto the cutting edge of the tool, which results in rapid degradation and deformation of the cutting tool. In order to control heat levels, water-based coolant must be injected directly between the cutter edge and material at high pressures and high volumes. This approach provides sufficient lubrication to reduce the coefficient of friction and overall production of heat, providing for extended tool life in titanium machining operations.
Watch this webinar to learn about effective cooling strategies for extended tool life in titanium machining. View Webinar
Outside of proper cooling technologies, the most significant means for extending tool life in titanium machining is the use of a reliable machine platform with the power and rigidity to maintain stable cutting conditions. Standard production machining centers typically lack the rigidity, torque and vibration damping technologies necessary to appropriately manage forces that occur during the machining of titanium. As such, a machine platform that’s purpose-built for titanium is a necessity for improving tool-life results.
Related Content
-
Temperatures in the Titanium Cut Zone
//29 min
Executive Summary
The superior strength-to-weight ratios and corrosion resistance of titanium alloys have led to an increasing demand for titanium components in the aerospace and petroleum industries. But titanium’s strength, low thermal conductivity and high chemical reactivity also make it difficult to machine. Controlling cutting temperature is particularly critical to achieving high-performance titanium machining.
This presentation reviews the latest research into cutting temperatures conducted at the Global Titanium R&D Center at Makino in Mason. The research is aimed at a better understanding of heat generation in order to optimize cutting conditions and select efficient cooling strategies to achieve maximum productivity, tool life and finished surface quality.
-
The Makino Cost ADVANTiGE
//10 min
Executive Summary
Makino is helping companies reduce part costs by offering tooling, processing and equipment improvements with machines such as its new T2 and T4 5-axis horizontal machining centers.
With the T-Series, tool life is increased and operating costs are lowered. With less tool inventory, you have lower tool replacement labor costs and better quality. Metal-removal rates are also increased, resulting in less machine time and lower operating costs. With that comes less capital investment, lower equipment maintenance costs, less manpower required to operate the machines, less work in process and increased part turnaround times.
This presentation details the primary methods for reducing part costs, including longer tool life and higher metal-removal rates. This presentation also offers productivity and cost per part comparisons for the T4 and demonstrates that by capitalizing on the advantages of higher metal-removal rates and additional tool life found in machines like the T4, companies can begin to see a significant impact on their bottom line and cost per part.
Mark Larson, Titanium R&D Team Leader, Makino
-
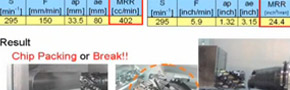
Test Cuts Demonstrate Benefits of Makino’s ADVANTiGE Technol…
//29 min
Click to View
Test Cuts Demonstrate Benefits of Makino’s ADVANTiGE Technology
//29 min
Executive Summary
Test Cuts Demonstrate Benefits of Makino’s ADVANTiGE Technology
This presentation provides several detailed part machining examples, including a pylon spar, edge frame and frame component, as well as various cutting techniques that are being used to make the T4 machining center even more productive. Each of the before and after part samples illustrate the ability of ADVANTiGE to provide four times the productivity and double the tool life in titanium machining.
Several high pressure, high volume coolants were tested on roughing, semi-finishing and finishing applications and are also demonstrated in this presentation. Tool wear and tool life are closely monitored and reported, ultimately showing the increase in tool life that Makino’s ADVANTiGE technology affords, an important component in reducing operational costs.
By breaking through these conventional limitations of low metal removal and limited tool life, Makino’s ADVANTiGE technology provides a degree of machining efficiency that no other Titanium technology has offered in the past.
Masayoshi Hirahata
Sitae Re Volupta Tquidus
//35min
Executive Summary
Evereprepudi dolorum eum excea et occus quias aut ea voluptatur antur assuscia nus, con re volupta tumqui que evenihita eostiatus experem quo ea destrum qui opta cum nessit abo. Neque volesto rionsequamus re solorpo ritium quatinc tecabo. Namet odior re simodigenis earchil inis ra con perumquis doluptassum nobis sim adissed eic tem estist ani doloressit aut adisinu lparibus dem as nulparumque prectio de cusaped itatend errorat laces accum rerum et asitae recus am, occuptaquos et ea impor rere, sintur, sin corecat.
Tionet landi repudae rferro ommos il earum vid et mil ius exped et mos et quo eosto blamet as esedit apelibu scitatur sum, explitia volupta tempor aut magnit, ommolendant, corum is elicipsunt que vel iliqui di audam eaquos num abo. Architem venihilicium di ommo odit eum in pe imi, optis et ped